As more automation drives processes and continuous manufacturing replaces traditional manual batch manufacturing, access to real-time streaming data will become critical to pharmaceutical, biologics and speciality fine chemical manufacturing operations. A basic data landscape for operations and activities that currently exists in various divisions within these industries is shown in figure 1.
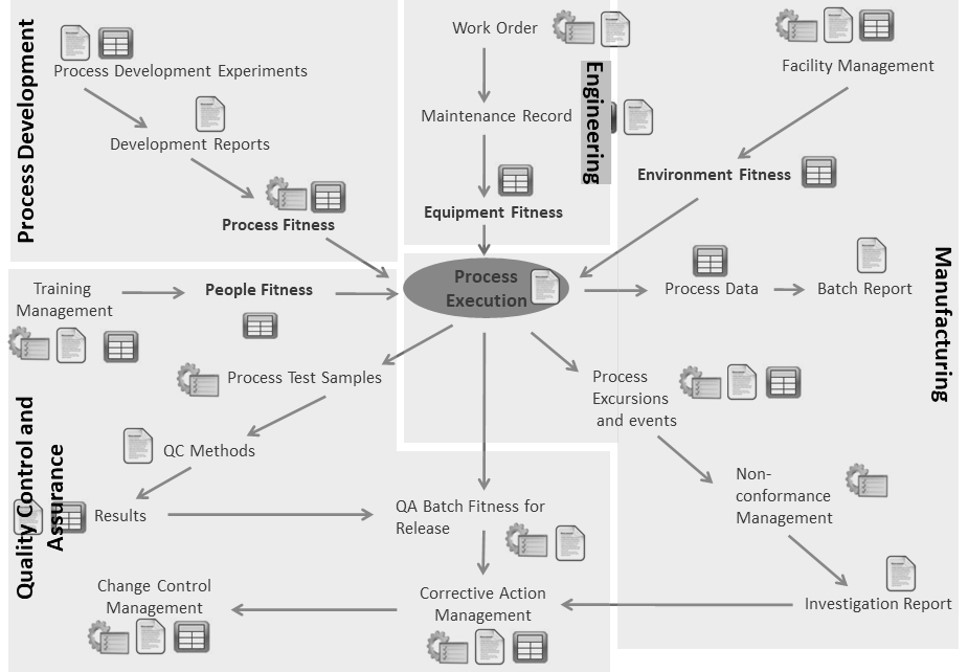
Figure 1: Process Data Landscape
Most of these operational activities may be captured in electronic systems created specifically for those activities are shown in Figure 2. There remains a difference between the OT (operational technology) systems (shown in yellow blocks) that are primarily associated with activities linking with the direct process machine interactions. The manual data entry or offline type of operational activities are associated with traditional IT systems shown in green blocks.
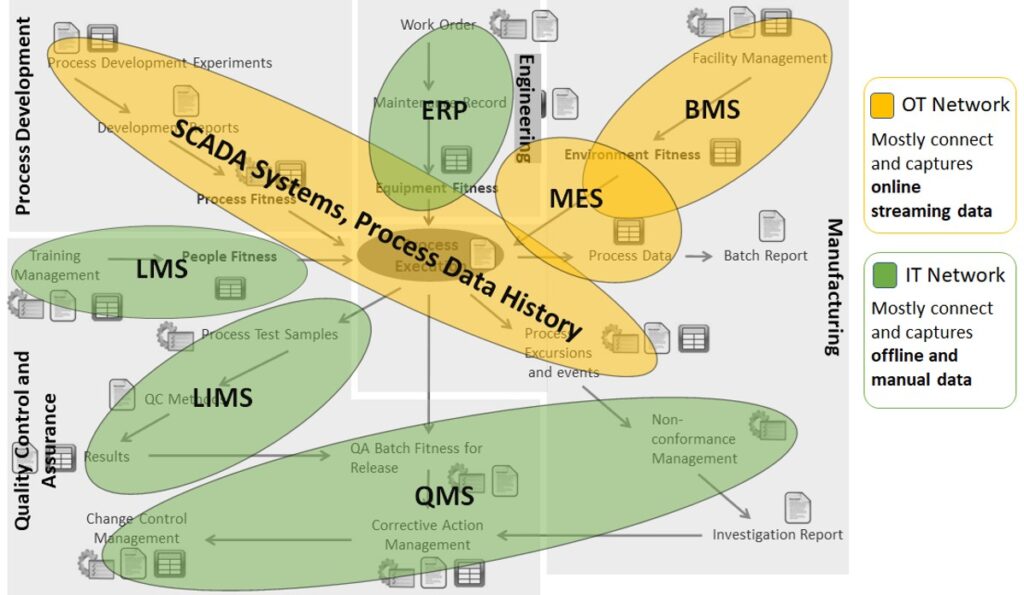
Figure 2: Typical IT and OT systems
The Current State
Typically, we have seen that IT systems which are not attached to a physical machine on the factory floor are now mostly either installed remotely in a local/corporate data-centre or are hosted as public cloud system using the new approaches of OS and/or Container Virtualization. The OT systems are however has not made to the newer ways of virtualizations and application deployments owing to physical limitations and non-availability of similar infrastructure near the plant floor. Figure 3 show where the current IT and OT systems are installed, operated, and maintained.
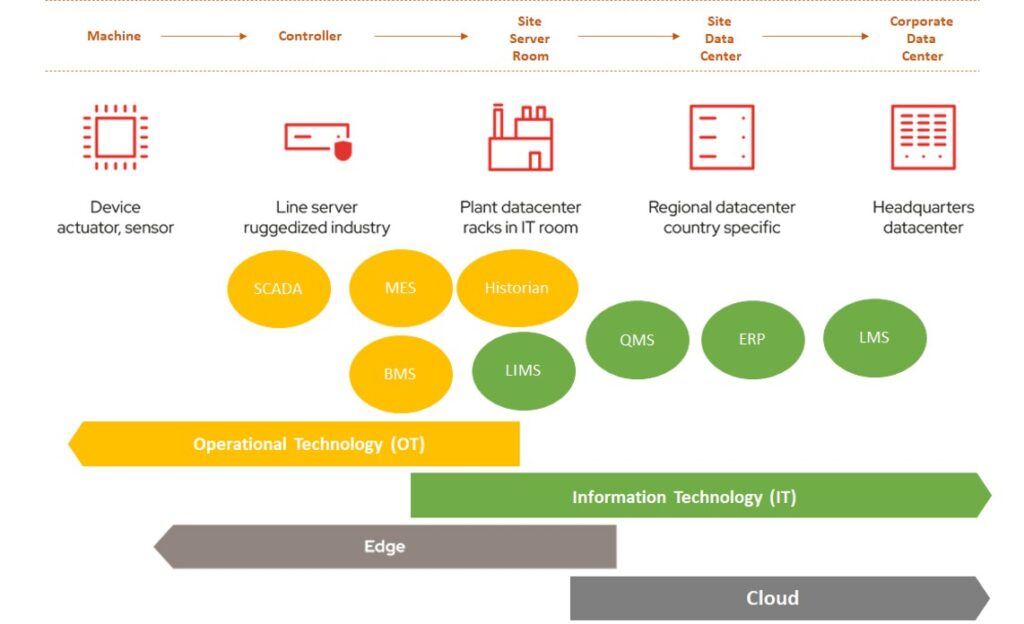
Figure 3: Current state of OT and IT systems deployment
Most of the current IT systems (green blocks in Figure 3) in the modern paradigm have been running on some sort of virtualized environment over VM or more recently containers. This required it to run on large array of physical servers that manage separate compute, network, storage stacks independently (see Figure 4). Either on-premise data centres or large cloud providers can only be able to provide this stack of resources.
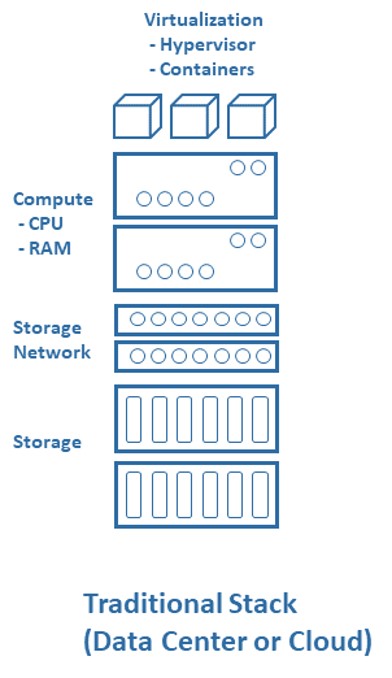
Figure 4: Infrastructure stack required for any typical IT system application
This is the primary reason why the OT systems which runs on small traditional machines with limited compute/storage and isolated networking has not transitioned itself to this new paradigm of application virtualizations. Also, this has been traditionally the main reason of divide between OT and IT systems and not being able to communicate data across each-other. Figure 5 below shows the current state of limitations of the computing infrastructure on the OT side owing the limited resources available on the factory floor.
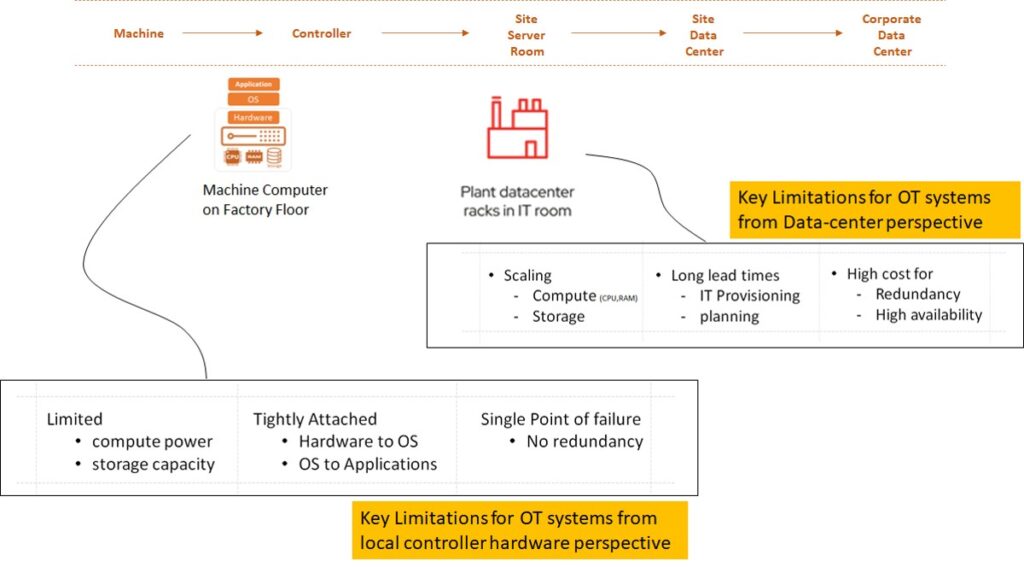
Figure 5: Limitations of current infrastructure for OT systems
What does cloud-native technologies offer?
The limitation mentioned in figure 5 above make a strong case to bring cloud native technologies to OT world owing to elastic compute, storage capability coupled with high redundancy and availability. Figure 6 shows many advantages cloud-native technologies can bring along with key enablers that can help bridge gap between OT and IT world.
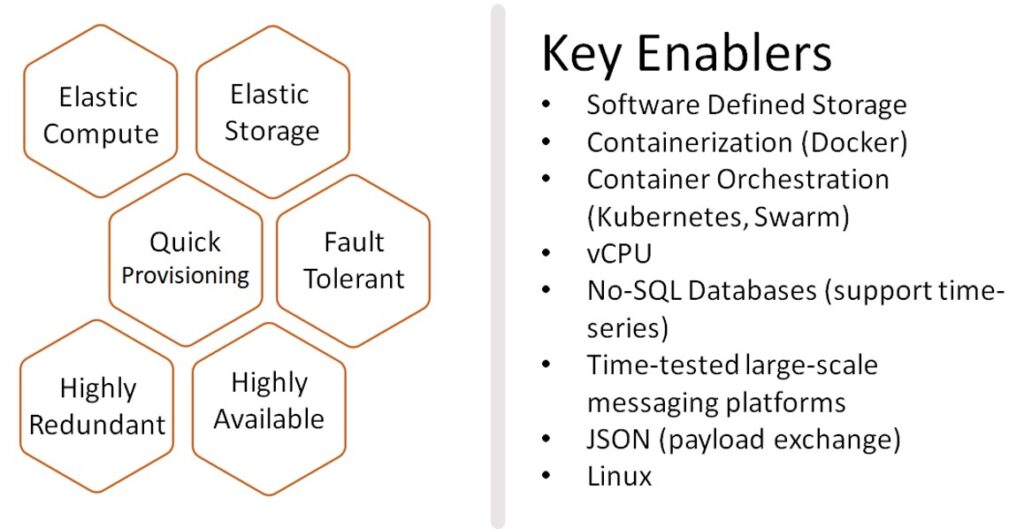
Figure 6: Key benefits and enablers that cloud native technologies provide
Why Hyperconverged Edge computing makes more sense for OT systems over moving them to cloud?
There are many limitations of moving OT systems to the public cloud system. Since the physical machines need to run mission critical processes, Figure 7 shows some key challenges that make case of keeping the OT systems on-premise.
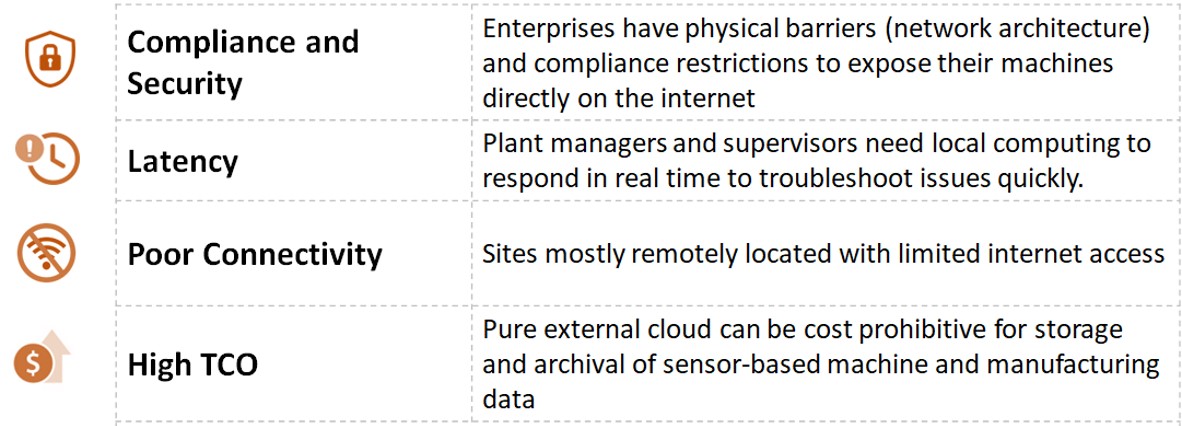
Figure 7: Why cloud will not work for OT systems?
Hyperconverged edge-computer clusters (Figure 8) could solve this challenge to bring the require compute and storage to the OT world where it is needed near the factory floor. In the near future we will begin seeing these hyperconverged systems will start making their way into factory floor to provide that vital link to create an interconnected factory floor of OT and IT systems that begins to start talking same language in terms of compute, storage and network.
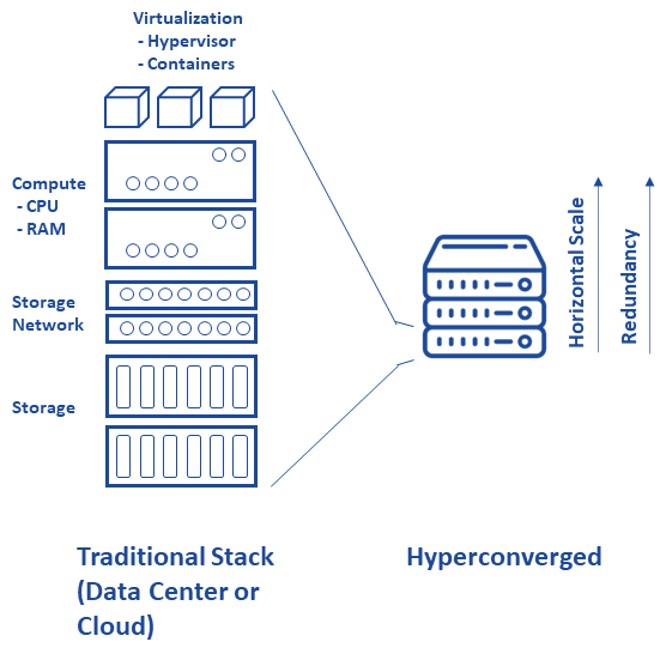
Figure 8: Hyperconverged Edge-computing cluster
Other benefits of adopting hyperconverged edge-computing infrastructure for OT-systems
- Benefits in the Validation Life-cycle
- Considerably reduce documentation and validation time-lines
- Uniform hyperconverged compute, Storage and networking
- Applications packaged within the minimal container environment
- Highly predictable and reproducible compute environment
- Decouple infrastructure with application qualification
- Faster introduction of new applications and changes to existing applications or processes
- Easier to make technology/infrastructure upgrades
- Considerably reduce documentation and validation time-lines
- Avoiding software driven single point of failures
- Considerably reduce system downtimes
- Replicated, Redundant Always-ON infrastructure
- LIVE computing hardware repairs/replacements/scaling possible with no process downtime
- Considerably reduce system downtimes
What Factorian Offers
We provide fully serviced plug and play data management software “Factorian” packaged and optimized to run on our edge computing devices build using commodity hardware and the hyperconverged cloud-native technologies described above. Factorian software platform provide easy way to connect and access data from your existing factory systems (SCADA, BMS, MES, PLCs). In a single platform you can begin archiving sensor and streaming data coming from all your factory floor systems. It also has the capability to connect to your IT systems to read any RDBMS databases (like LIMS or ERP) so that data from IT and OT systems can be accessed and alerted together utilizing its innovative event driven architecture. As you need to add more systems and factory suites you simply need to stack more devices or add new cluster stacks. The edge-cluster devices are delivered as fully serviced annual subscription.